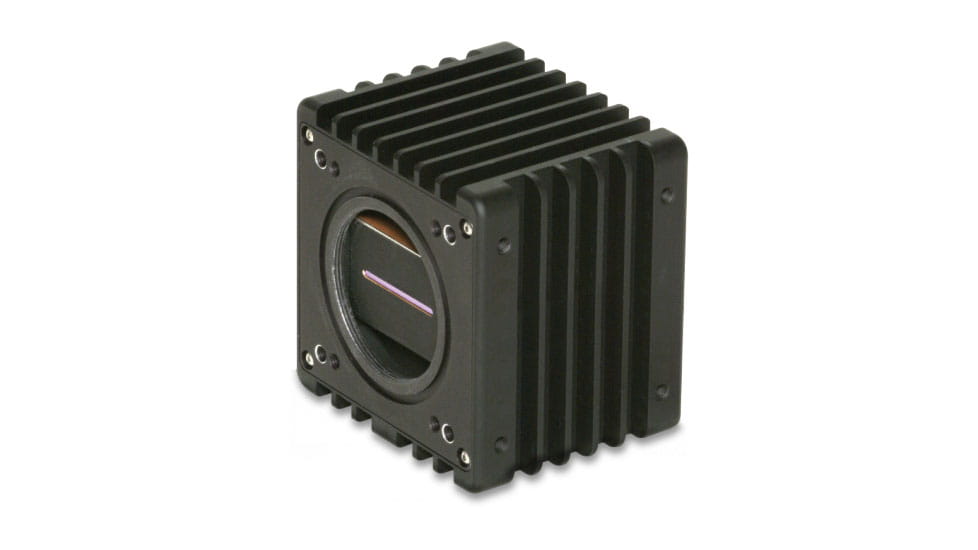
Manufacturers of glass hollowware have long sought a way to pick out defective product at the hot end of their process, while the pieces are still above 200ºC. At that glass inspection stage, rejects are identified, then shunted aside and reprocessed efficiently, greatly reducing scrap. Experimentation has shown that the peak performance range of lattice-matched InGaAs SWIR cameras is ideal for imaging temperature gradients as the hollowware cools. Unlike thermal cameras, SWIR cameras can image through glass, allowing operators to inspect both the interior and exterior walls of the bottle, as well as monitor the temperature uniformity and cooling rate of the material.
These images allow glassmakers to prevent shattering due to uneven cooling or unmelted raw materials. Sometimes a manufacturing flaw or contamination creates a web of hair-like glass filaments that crisscross the inside of the bottle which must be identified at the glass inspection stage of the molding process. When cooled and hardened, these filaments fracture into shards that fall to the bottom of the container, where they could remain through the end of the fill process. A SWIR integrated glass inspection system can detect a temperature differential between the filaments and the bottle wall. Consequently, the users' glass inspection systems activate an error signal that blows the bad bottle off the line and shuts down the responsible mold. The end result is less wasted material and a lower probability of injury to the consumer.
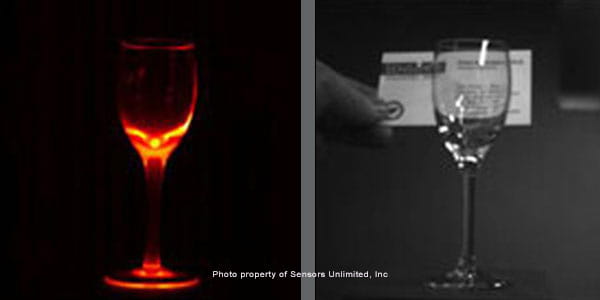
On the left, a hot wine glass is imaged in false color imaged simulating glass inspection using a Sensors Unlimited InGaAs camera. The signal levels can be calibrated to temperature; in this instance, the hottest part of the glass is 330ºC. On the right, the same glass at the same temperature is shown with a business card behind it, demonstrating that hot glass is completely transparent in the SWIR band.
Recommended product categories
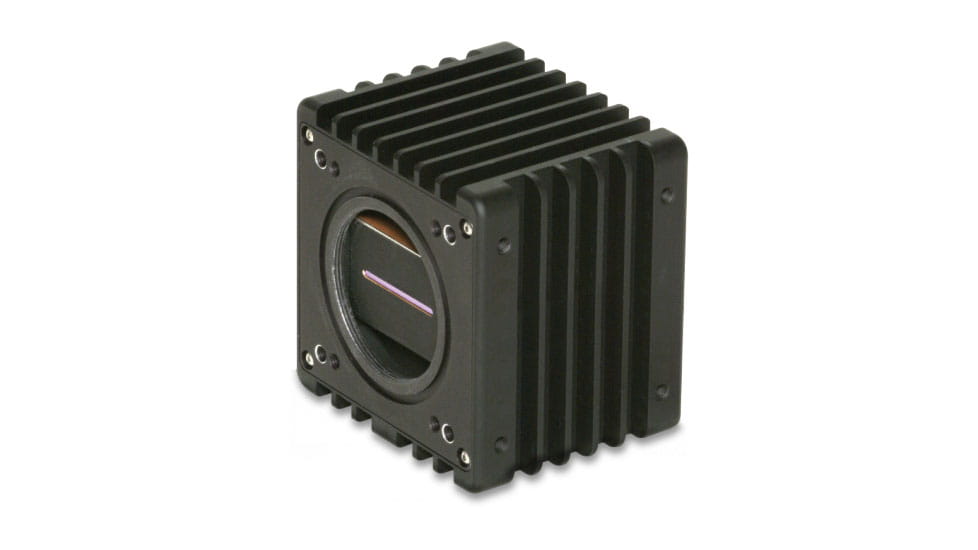
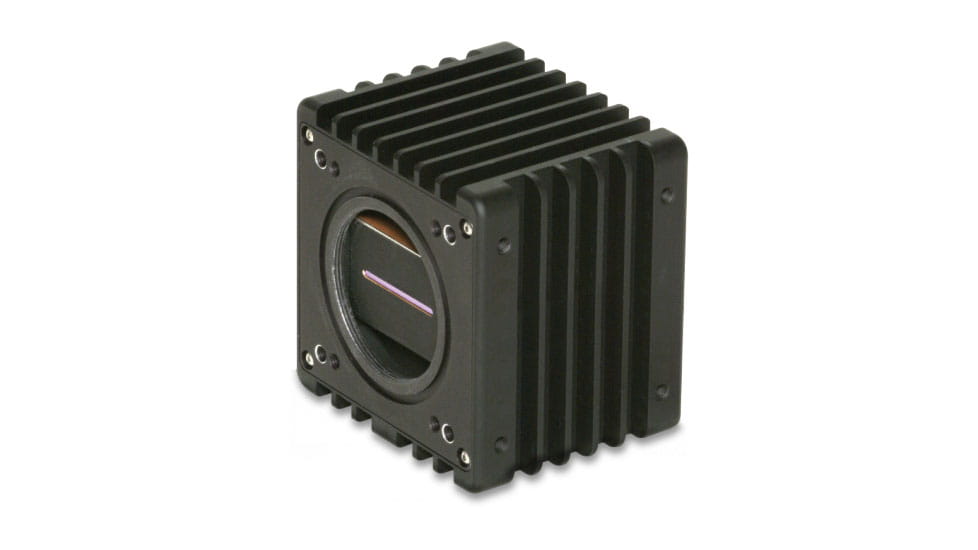
1024LDH2 Linescan Camera
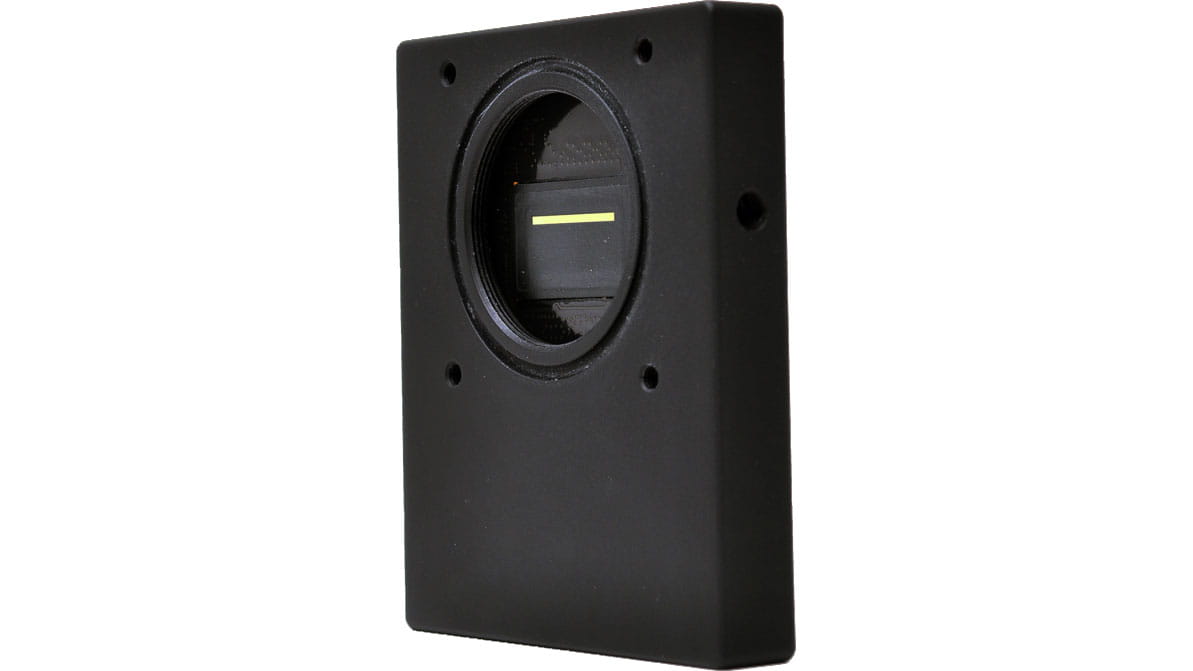