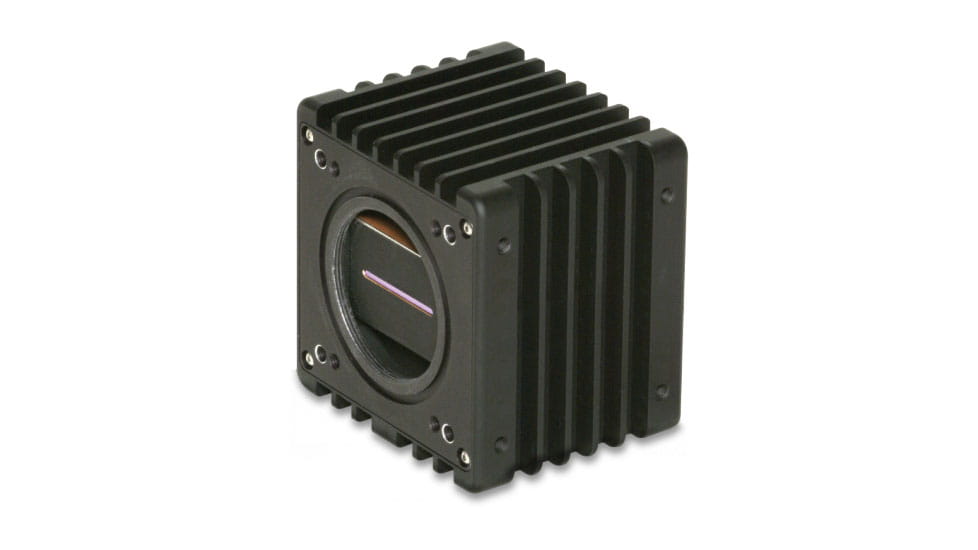
The use of InGaAs short wave infrared (SWIR) cameras for industrial process monitoring and thermography has many advantages that offer system integrators a new imaging tool and end- users new ways to improve quality in production. InGaAs cameras provide users with an instrument to detect thermal emission and reflected light in the 900 nm to 1700 nm wavelength range. These cameras have proven to be effective at detecting and monitoring slag impurities in molten metal because of the emmisivity differences between the slag and metal at that temperature.
With a near infrared slag monitoring system, an industrial ladle pours only pure metal and no impurities, see below:

One of the challenges in metal production is eliminating the impurities that form as end users process the molten metal (typically 980 to 1650 degrees C). These impurities are known as slag. An imager that can accurately detect the difference between the slag and molten metal can save processing plants valuable time and material. InGaAs cameras detect emissivity differences between the hot metal and the slag, which provides operators with necessary information on when to end the process. This, in turn, helps prevent unwanted impurities from contaminating the metal. Missing this process end point can affect steel quality and translates directly into higher cost of production for manufacturing facilities.
InGaAs cameras have proven themselves in this area and have competitive advantages over some of the competing imaging solutions, including the ability to image through glass lenses and glass windows. This allows the camera to be protected in enclosures while allowing for an inexpensive glass window (versus an expensive Germanium or sapphire window) to keep flying debris from damaging the camera.
Recommended product categories
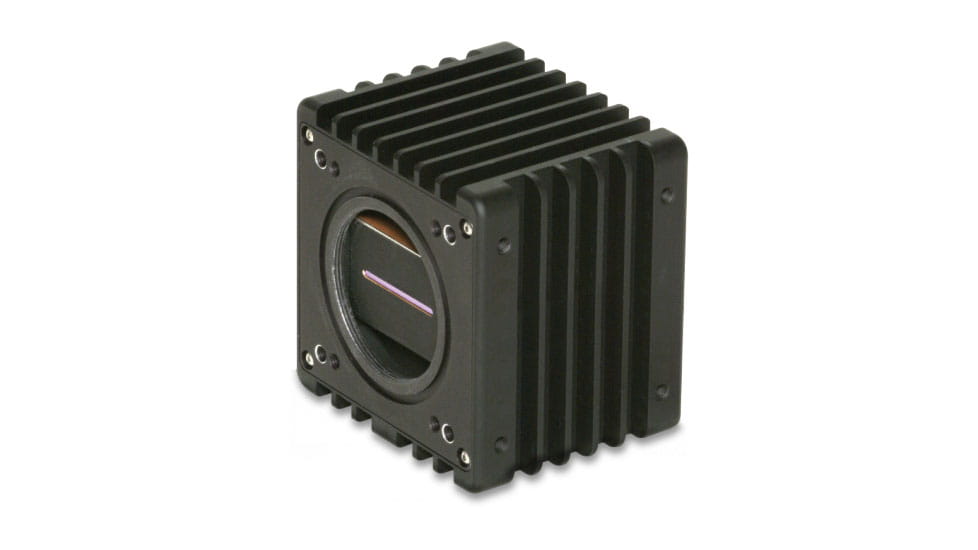
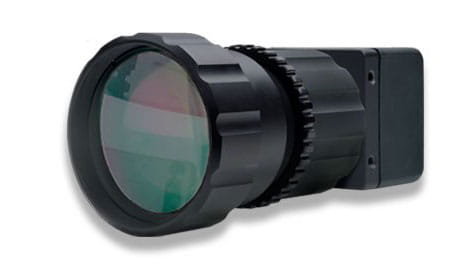